导读: 注塑设备智能化成型加工技术包涵多支智能化成型加工技术,而这些技术根据成型加工的发展、科技进步以及人们认识的提高处于不断开发中。
智能化能耗技术
能源成本占据生产设备整个使用成本的90%以上。节约成型加工能耗一直是注塑成型加工科技进步的重点,也是实现注塑设备绿色化的重点。最理想的能耗就是注塑的设备能耗匹配于塑料由原料熔融成为制品所吸收的热能。
注射能耗即注射压力和注射速度的两个参数之积,目前注塑成型加工的这两个技术参数都为人为设定,具有很大的盲目性,而且都为开环运行,这两个技术参数的设定值往往大于模腔内成型制品的实际需要值,不但浪费能量,而且影响制品的表观质量及内在物理性能。智能化控制可把模腔内成型制品不同时间所需的熔融料的压力和流速通过检测系统反馈给中央控制系统,中央控制系统根据信息发出指令调整注射压力和注射速度,高速动态反映性能的注射机构在指令下迅速作出反应,实现注射参数匹配于成型制品所需的参数,达到最佳的动力驱动能耗。
菲尼克斯公司的能量管理模块(EMM)具备获取能量数据和监视能量数据的作用,通过现场总线或以太网提供数据采集和传输,Inline I/O模块之间的连接实现了一种从能量消耗点到控制层系统的无缝信息流,实现能效智能化管理,降低电能消耗。
智能化保压技术
基于模腔熔体温度的保压控制 (P-T)。模内熔体的温度是时间的函数,该温度是通过传感器进行连续地检测来获得的。利用型腔温度作为信号对保压过程进行控制(P-T)比传统的时间控制(P-t)具有更好的适应性和控制精度,经对比试验表明,P-T控制得到的重量重复精度0.0785%,比时间控制方式的0.1843%的重复精度高出很多。
基于模腔熔体压力的保压控制。传统注塑机保压控制为从注射压力到保压压力采用位置切换,而到保压阶段就从位置切换转入用时间切换多级保压压力的控制方法,其精度和稳定性都较差。利用依靠检测模腔压力来实现压力切换的,即通过一个预先设定的程序来控制。也就是切换点的压力值先存储在控制系统中,其后转换成逻辑控制信号,如果模腔中的压力与设定值相同,则立即切换到保压控制。
压力及温度传感器的性能直接关系保压质量的控制水平。
智能化能量回收应用技术
1、智能化全电动注塑机制动能回收应用技术
这项技术在全电动注塑机上得到开发和应用。Netstal的ELION系列全电动注塑机,把伺服电机制动过程产生的能量直接进入过渡电路,储存在电容电路中,这意味着产生的制动能量不必转化成热量,尤其是在注射循环期间,可以成为总能耗的一个重要部分。例如,当塑化过程发生在模具打开时,产生的制动能量可从过渡电路中汲取旋转螺杆所需的能量。因此,该能量并不是取自电源供应网路,并且产生的能耗相应减少。生产成型塑料花瓶表明,从伺服电机制动过程直接进入过渡电路的能量占所需循环能量的15%,成型总能耗为0.25kWh/kg。对熔化塑料所需能量的计算表明:这仅比每个循环所需的总能量略少一点。同样,驱动机器所需的能量几乎全部来自各轴的制动过程,并未通过制动电阻转化为热量。与液压注塑机相比,ELION系列注塑机能耗减少了70%,比常规的全电动注塑机能耗低10%以上。
2、智能化塑化加热辐射能回收应用技术
把塑化机筒的电阻丝加热圈辐射散发的热量收集起来,送入干燥器料斗,转为烘料热量使用,节省干燥料斗原需电加热供给的烘料热能。整个系统为气体循环的封闭系统,采用独立式的双重过滤进气系统,机筒集风罩具有空气过滤功能,保证了能量交换媒体的热风空气的清洁度。系统根据设定的干燥温度及收集的散发热量进行分析对比,智能控制冷、热气体量的混合比,标准原料的干燥度。广东某塑料厂安装了深圳市某公司开发的注塑机热能回收利用的干燥装置系统,节能效果显著。该企业有30多台注塑机,机筒加热功率5kW,耗电5kW·h/h,每天工作16小时,每月26个工作日,月耗电:30台×5×16×26=62400 kW·h;减去恒温消耗功率,以负载功率75%计,月耗电46800 kW·h(其实恒温工作时也耗电),每度电0.80元,年节省电费45万元。
3、智能化伺服电机驱动油泵制动能回收应用技术
伺服电机驱动油泵的高效节能技术在国内制造的注塑机上得到广泛应用,进一步节能似乎成了发展的瓶颈。
大同机械集团的东华机械有限公司智能化伺服电机驱动油泵制动能回收应用技术是国内注塑机行业首创的一项专利技术,具有自动识别储能和输能的工艺环节。在系统中增加伺服驱动制动回收单元,达到存储伺服永磁同步电机在刹车制动过程中产生的电能,同时能够将此电能释放到注塑机的工作过程中。在直流母线上串入伺服驱动制动回收单元,以减少制动电阻消耗的能量。制动电阻和伺服驱动制动回收单元并联一起,用以消耗伺服驱动制动回收单元储存完成后多余的电能,保护伺服驱动制动单元和伺服驱动系统。伺服电机在刹车及减速过程中产生的能量转换为电能,通过伺服驱动器中的逆变模块单元和直流母线,将电能存储在伺服驱动制动回收单元中。而当系统重新提供电能开始工作时,伺服驱动制动回收单元中的电能首先释放,能源再生单元储存的能量将通过直流母线回放到系统中,实现储存能量和释放能量的双向作用,当电压低于整流模块输入的电压时,才使用外部电能,从而达到节能的目的,能效提高3~5%。
智能化实时塑化温度控制技术
计算机本身具有PID闭环精确控制塑化温度功能。塑化加热温度实时性及实时检测性,直接关系到实现实时的智能化加热温度的灵敏精确控制。
实时塑化加热系统。传统的电阻丝加热原理是电阻丝本身产生高温,然后热量再慢慢的从加热圈本体传导到料筒外表面,然后再从机筒高温区传导到机筒的中心低温区,速度缓慢,并且位于料筒中心的塑料实际温度和料筒表面温度有较大误差,当塑料温度达到要求时虽然电阻丝停止加热,由于存在温度误差,料筒表面仍然继续向料筒内部传导热量,导致温度控制不准确,热电偶不能实时反映塑化温度,提供给电脑的温度数据与实时塑化温度存在误差,造成电脑在分析、判断、决策塑化温度的错误。达不到智能化塑化温度的实时性的动态反映性能。
高频电磁感应实时加热系统。高频电磁感应使机筒本身自行高速发热,热能是由料筒金属整体产生,温度控制实时性准确,料筒内外温度一致,实现对塑化温度的高动态反映控制。电磁感应线圈对机筒来说是零热容,加热直接作用于机筒,这样感应加热所需的时间会更少,沿机筒长度和圆周方向的感应热分布非常均匀,其快速响应转化为更加均匀的机筒温度。温度控制器将动力输入到感应加热器时,输入到机筒的热量几乎瞬时达到最大值,当动力被控制器切断时,热量输入很快降至零。
纳米红外实时加热系统。纳米红外加热系统,发热体采用新型高分子纳米发热合金材料,加热圈表面经高分子远红外材料做特殊处理后,能够产生特定波长红外线,有效提升加热速度,升温速度比传统电热圈快20%以上;热惯性小,温控精度可达±1℃。在通电时只产生热辐射,热量通过红外辐射传导,不产生高频辐射,无紫外线。
实时加热系统同时具有高效节能、环保、清洁生产性能。传热效率在99%以上;加热圈的表面温度仅为50-70℃,对环境温度影响小,且能有效的降低工作车间的室温5-10℃;节能率高达30%-80%。由于表面温度低,它不会烧焦吸附在它表面的异物:如塑料颗粒、油污、灰尘等,不会产生有害气体。完全避免传统加热方式带来的因表面高温而造成的烧伤、烫伤事故的发生,更杜绝了因表面高温引燃附着物发生不安全事故。
智能化塑化背压技术
螺杆在预塑时,计量室中熔体的压强称为背压。背压控制是为了减少轴向温差,控制熔体密度,达到塑化精确计量。机头储料腔熔融料密度精度是实现精确计量的标志参数,因此其储料腔的熔融料的压力直接反映出其密度精度。
现行塑化背压都是人为设定的开环系统,是通过预选油压的多级控制来实现的。当螺杆预塑时,其在物料的作用下要后退,这就会使注射油缸腔的回油经过背压阀流回油箱,因此通过调整背压阀在螺杆不同位置时的泄油压力间接起到调节螺杆头部熔体的压力(背压),从而使其轴向温差得到调节。这种间接的开环的背压调节不能实现理想塑化质量下的精确计量。
智能化背压技术的塑化背压根据压力传感器检测机头储料腔的熔融料压力信息作为控制背压的指令,直接反馈与设定的压力进行比较,自动跟踪变化,利用储存注塑合格品的压力波形,并在射出—保压过程中按合格品压力波形进行追踪控制的功能,提高塑化质量精度。日本东洋的背压自动跟踪技术,在si-100(C75)应用表明,塑化计量精度提高50%以上。
智能化背压技术为实现智能化计量创造了前提。智能化计量就是要实现不论在何种条件下,反映出真实的塑化计量。根据塑化PVT原理,熔融料在不同温度及压力下,具有不同的比容,质量也不同。目前塑化计量,只是计螺杆的位移量,实际上达不到塑化的真实计量。智能化背压达到了储料腔的熔融料的温度、压力和热比容一致,保证了塑化计量的精确性。智能化计量系统只要选取三个参数中的一个参数进行分析、推理、决策,确定塑化螺杆的位移,达到真实的塑化质量值。
智能化配混喂料技术
塑化原料中不同成分比例经常需要按照产品配方改变,实时控制添加剂含量很重要,这就要求配混喂料系统能提供自由灵活的可变换原料的精确配置系统。
喂料配混系统智能化技术主要体现:精确控制塑化原料的组成达到提高制品质量,精确计量实现资源(塑料原料、辅料、添加剂等)节约型加工。
失重式计量配混料系统
失重是计量配混料系统基于称重技术原理而建立的先进的混配料及质量控制的喂料系统,系统由失重式计量配混料机和控制系统组成,适用于多种新料的计量配混喂料。
系统采用计算机控制,控制运行状态、工艺配方、输入参数,实时监测原料的挤出量,控制挤出机螺杆转速,使挤出量保持恒定和严格控制在工艺要求内。原料密度变化、松散度的变化、粒料形状大小的不同以及原料流动性质的差异,所引起的物料产量的变化,原料挤出量检测采用连续失重式称重原理,自动称重喂料系统予以记录并得到控制,通常可节省 2~5 %的原料。同时自动称重喂料系统完全由PLC实现自动控制,具有通信功能,可以由主计算机设定、监控生产的各项参数,例如各层挤出的配比、产量等数据,为生产的自动化提供保证。上海环球机械有限公司失重式计量配混料系统,实时在线动态监测,通过智能软件的计算和分析,可按设定要求对工艺参数自动优化和调整,最多可实现对8种物料的配混控制,适用于颗粒状物料及流动性较好的不规则物料喂料的单螺杆失重式计量喂料机最大能力达到1000kg/h,适用于颗粒状物料、粉料及流动性较差的不规则物料喂料的双螺杆失重式计量喂料机的最大能力达到2500kg/h。
重力式计量配混料系统
重力式计量配混料系统适用于新料、回料、色母粒、添加剂等计量配混喂料。
美奎亚洲推出一种先进的重力式喂料机,系统特有的精确失重称量功能连续追踪和调整投料误差,不受新加入物料的干扰;控制器调节螺旋加料器的电机转速,自动适应螺杆扭矩、工厂电压或原料的变化。上海环球机械有限公司重力式计量配混料系统,系统根据设定值最大运行,无需人为计算物料的比例,精度达到±1%,组份可达6组,最大喂料能力达到1500kg/h。
智能化调模技术
调模系统的作用,是当生产过程中更换产品需采用不同厚度的模具时,调节轴向容模量的大小,同时使合模系统对模具产生所要求的锁模力。
智能化调模的目的是合模机构的锁模与模具成型加工模腔产生的涨模力达到最佳的匹配状态,不但保护了模具及延长模具的使用寿命,而且降低了锁模能耗。反映两者之间是否达到最佳匹配的表征是模具在注塑过程中,模具分型面涨模量是否处于临界状态,所以模具分型面的涨模量作为智能化调模的检测参数。模具在注塑成型过程中的模温波动应处于一定范围内,以不产生影响锁模力的因数。
成型制品检测智能化技术
注塑成型加工的目的是得到合格的塑料制品,外观质量是塑料制品质量的主要表征。智能化视觉技术检测制品在成型加工链环节中处于越来越重要的地位。视觉系统可先采集标准产品,而后针对需检测的产品进行对比分析,确定是否合格,检测过程既可在产品注塑刚完成后进行,也可以单独检测,做出分析,为中央控制系统提供准确、可靠的数据支持。中央控制系统根据视觉反馈信息作出分析、调整成型加工工艺参数,达到合格的产品。德国ISRA表面视觉公司Smash模块化检测系统,智能探测能有效扫描塑料薄片产品表面缺陷,并进行自动分析,以确定缺陷产生的原因,从而有助于生产者防止缺陷的产生,提高产品质量和生产率。
SmartScope Flash 500自动尺寸测量系统,具有多个带有可触发探头的传感器,配备了自动校正的AccuCentric 12倍电动变焦距头,用于影像测量,可对较难成像的部件特征进行触觉测量,还有用于测量非接触式表面轮廓的TTL、DRS激光以及彩虹探头扫描白光传感器,还提供可以获取几毫克探测压力数据点的独一无二的羽毛探针微探针传感器。Ohaus公司Navigator XT系列无接触质量测定仪,具有两个无接触式红外传感器,不要触摸按键,36种功能组合,适应于计数、百分比称量,重量复核、显示保留和累积/求和的应用。
(版权声明:“振业注塑汇”所推送文章,除非确实无法确认,我们都会注明作者和来源,如有侵权,请联系我们及时处理)
振业注塑咨询,针对注塑企业在发展不同阶段存在的管理痛点提供定制化的咨询服务和解决方案,从诊断开始——方案策划——方案实施——项目后服务一站式解决企业所存在的问题。
--- THE END ---
精益注塑 zy-plas
精益注塑|专注于塑料行业服务
助力工厂改善致电:0755-28152581
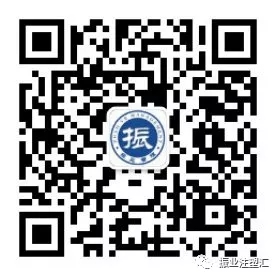
振业注塑汇
海量的注塑干货,供您任意学习分享,注塑实战实例最多的公众号!