3D打印和增材制造是国务院“中国制造2025”重要的产业发展方向。3D增材制造的技术,最大的特点之一就是它可以给我们起到我们能够制造多品种、小批量,甚至个性化的模式。增材技术既做到多品种、小批量,甚至个性化,但是它不增加成本,不降低生产速度。(杨氏注塑法)
而对于这项技术而言,最为重要的就是设备和材料,于是在政策的扶持下,西安建立了增材制造研究院,确定为国内增材制造的制造业创新中心。当然,除了制造之外,医疗,建筑以及教育也是这项技术能发挥重要作用的领域。
近日,由北京丰台科技园建设发展有限公司主办的一场3D打印产业高峰论坛,分享了这项技术在行业内的具体应用场景。钛媒体记者根据各方专家和学者的分享汇总整理出了以下观点:

义肢器械打印:可定制性更强,更安全
在医学领域,3D打印由于其可定制性高,在无需模具的情况下,可以用来打印诸如义眼,牙齿等等器官。这些都是完全定制化的,能做到立等可取,如果增加效率仅仅需要增加打印设备即可。同时,也能形成一定的规模,可能未来器官打印也能通过App进行预约。
除了打印这种义肢之外,3D 打印技术更重要的一项用途在于辅助规划手术。这并不是打印一个模型那么简单,需要一定的精细度,因为它能提供更多的信息给医生,进行高难度手术的规划。在骨科,这一技术已经被广泛地应用到了打印骨头和打印用于固定骨头的倒板。
过去使用石膏,现在使用轻巧的支架。低温塑料板能很好兼顾固定的紧凑性和轻便性。比如颈椎部分的支撑,过去是常规的像海面一样贴着,现在可以用3D打印做个性化支撑;烧伤的病人过去疤痕会扩展,现在可以用一个工具固定,防止疤痕蔓延。
软组织外科也非常积极的进入到这个领域应用,比如母子脾肝技术,没有3D打印,光靠影像数字很难支持。有了它,就可以知道血管之间的吻合状态。通过3D打印看到血管的关系,可以减少对无关血管的伤害,直接把伤害肿瘤切除。

现在3D打印模型已经能从简单的到复杂了,为了这个复杂科研人员做了很多器官的测试,开发了与人类皮肤肌肉几乎一致的材料。这些打印器官还可以组合成完整的人体模型支持医院使用,特别是高难度手术的训练――比如在脊柱微创方面的仿真人体,在普通外科的仿真人体,介入治疗的仿真人体。
在齿科,患者口腔里使用的材料则成了最大的问题:必须具备生物亲和性,同时还有抗菌。因为口腔中间抗菌特别重要,口腔里面戴一些东西会引发其它疾病,矫正牙齿的时候如果刷不干净,很容易造成牙齿的损坏。
制作口腔内材料的设备主要是光敏树脂,而国内用的所有的光敏树脂材料全部都是进口的,这个树脂要求是低黏度、低收缩。树脂的收缩率在口腔中的应用特别重要。国内已经开始在这方面进行探索了。目前,研究人员通过树脂配方的调控,做出来一种接近树脂的自制树脂,添加了载银抗菌剂。
在3D打印领域各国都缺乏医疗应用领域的法规,都在摸索的阶段,但是这个技术在医疗领域的应用也是得到各个国家的高度重视,都在推动技术的应用和医疗领域的法规建设。今年12月月初FDA正式发布的增材制造技术的技术考量,相当于中国的技术审评的指导原则,里面特别详细的把3D打印技术,考虑到哪些风险点和要求,非常详细。
标准化工作重要性毋庸置疑,首先确立标准,行业有据可依,审评也是有据可依。现阶段特别缺乏3D打印用于医疗领域的质量标准。

建筑行业:初步探索阶段
人类的建筑历史是从石头木头开始的,到了近代才出现当前的主流钢筋混凝土结构建筑,再就是上世纪20年代的“玻璃摩天轮”――以钢结构和玻璃结构为基础建造的。那么建筑物有没有可能被打印出来?
国内外已有不少的建筑事务所和建筑公司采用3D打印制造技术,为建筑设计项目,关键的像钢结构的构建,定制结构的连接,以及专门的外墙面板等等,设计整体打印建筑,其应用范围的扩展越来越广。
目前在世界范围以内,对3D打印建筑都处于非常初步的探索阶段。这其中存在很多问题,其中最重要的问题就是材料问题。目前打印出来的混凝土的强度和安全性都存在一定的问题。混凝土材料最好的性能是受压,能够承受压力,不会垮,但并不能弯曲――这是依靠钢筋实现的。
3D混凝土打印不可能打印出钢筋,仅仅打印出混凝土,这个是它最大的缺陷。要么先放好钢筋再打印混凝土,或者反之,先打印再插入钢筋。这与我们传统建筑的方式相差不远。
目前国际上已经开始探索无需钢筋做支撑,又能实现这样功能材料了。纳米混凝土是当下的答案。基于智能打印的方式,通过这种材料,还能实现多维度的打印,它就能打印各种不同形式的,满足个性化需求的形态,通过机械臂实现多维的空中打印,还有更多的方式,把这些问题解决了,房屋的建造,这种不规则形状将会成为可能。
房屋是一个系统,包含着各种结构,需要经过各道工序,比如防水,保温,装饰等等如何将之结合到一块,才能实现房屋的建造,最终才能走向建筑的工业化。最重要的是房屋打印的时候,用什么样的设备。现在通过3D打印建造构筑物的时候,无论大小都需要门式框架,上面有打印头,如果打一层两层,框架可以通过结构做出来。如果要打印高层,或者打印更高的建筑,这个门式的框架就非常高,这就需要考虑机械上的可能性。

3D打印与铸锻结合:降低成本,提升强度
回顾一下古代的铸锻在中国有很长的历史,先铸锭再去打,而且不是锻打就能完成,需要反复锻打。反复的锻打才能够消除铸造的缺陷,使晶粒细小均匀。现代工艺也是如此,同时这个过程中还需要不断地加热,保证金属处于可锻造状态。
开放式的加工过程热量消耗很大,而且是重污染的过程。在这种生产方式是全世界通用的,先铸后锻,流程很长,反复锻造加热能耗大,污染重,需要整体轻量化制造的趋势下,依赖大型锻机且越来越大(8-15万吨),投资巨大。首先要铸锭,包括零件所有的尺寸,最后得出的零件要削掉很多部分,特别在航空航天器件,材料利用率很低。同时一个零件需要根据不同的功能,采用不同的材料。
3D打印技术能缩短制作流程,但是它在工业化应用的最大障碍,就是其自身的缺陷――有铸无锻,性能及可能性难及锻件,抑制变形和破裂难度大,同时目前效率不及传统工艺,成本也还降不下来。
突破技术自身缺陷的方式在于改变国内外传统制造铸锻分离的制作方式,实现铸锻合一,边熔边锻。用一台设备、金属丝及很小压力得到锻件,实现短流程、单机轻载、节能省材的绿色制造。攻克传统铸锻无法沿轮廓数字化成形的难题,实现铸锻铣一体数字化。过去需要长流程、多台设备的铸锻,现在只用一台设备输入金属丝就可以得到。
在过去铸造过程中,普通铸锻的零件在冷却过程中,非常容易产生裂纹,成品率不到10%。通过这样的技术可以百分之百的做出来,并且没有缺陷。千百年来发展起来的铸锻技术,通过与3D打印技术的结合,获得了新生。
轿车翼子板的冲压成型模具也可以采用3D打印技术。这种模具实现了模具表面为模具钢,内部大部分是铸钢,大大降低了成本――大部分用一般材料,少部分用很好的材料。不光是模具,用材料非常昂贵的阀方面,仅仅在材料上就有压倒性的竞争优势。将3D打印固有的住装晶变成均匀等轴细晶,形与质并行创制,性能超过传统锻件。
3D打印是一个高度依赖材料和设备的技术领域,整个行业的发展很大程度取决于如何找到成本更低,易于使用的材料。在行业发展的初期3D打印应该做减法,集中专注于几个领域,才能更多地发展。同时也要用工业手段解决个性化问题,使3D打印行业变成正常的行业,有前途的行业。

最后,也是最重要的一点,3D打印还处于发展初期,在很多领域都还没建立行之有效的标准,这需要一定的时间去探索和实践。
我们擅长:
深圳振业企业管理咨询有公司服务宗旨:为注塑企业推广科学注塑、精益注塑的理念,推动注塑企业技术及管理的合理化、简单化、标准化。建立“高效、稳健、低成本、快反应”的工厂运作体系。提高生产效率,降低注塑制造过程中的变异,降低成本,缩短订单反应时间,减少现金流占用,最终增强注塑企业综合的竞争力!
--- THE END ---
精益注塑 zy-plas
精益注塑|专注于塑料行业服务
助力工厂改善致电:0755-28152581
振业注塑汇
海量的注塑干货,供您任意学习分享,注塑实战实例最多的公众号!
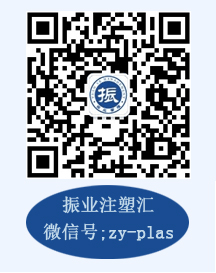
更多原创文章,请关注微信公众号:振业注塑汇