【振业注塑咨询】我们认为轻量化将伴随着汽车的电动化、智能化,成为未来十年新能源汽车发展的重点。
《中国制造2025》中提出:“继续支持电动汽车、燃料电池汽车发展,掌握汽车低碳化、信息化、智能化核心技术,提升动力电池、驱动电机、高效内燃机、先进变速器、轻量化材料、智能控制等核心技术的工程化和产业化能力,形成从关键零部件到整车的完整工业体系和创新体系,推动自主品牌节能与新能源汽车同国际先进水平接轨。我们认为轻量化将伴随着汽车的电动化、智能化,成为未来十年新能源汽车发展的重点。
1、新能源汽车轻量化的必要性
汽车的行驶阻力与车重成正比,车重增加,会使汽车的油耗大部分消耗在自重上,在100公里时速以下,重量因素决定80%的油耗;时速100公里以上,风阻就成为油耗的主要因素。国际铝业协会报告指出,汽车自重每减少10%,燃油消耗可降低6%~8%。因此,轻量化是节油的重要途径。
电动汽车由于特殊的电池驱动结构,相比传统汽车,由于受电池重量及续航里程因素的影响,对车重更加敏感。新能源汽车电池的重量增加了数百公斤,需要针对车身的耐久性能做特殊设计;同时使用了额外的高压电,对其安全性要求更高,包括整车的密封、车身的结构、更苛刻的防水要求等。所有这些要求都对新能源汽车的轻量化开发提出了巨大的挑战。
目前,能够使用的动力电池的单位比能量与传统汽车使用液体燃料的单位比能量差距巨大,动力电池系统通常占整车总质量的30%-40%。这就决定了电动汽车在与传统汽车同等排放量的单位能耗(电耗量/100km)下,不能像传统汽车那样靠一次补充能量来实现长距离的行驶。因此,电动汽车必须在电气化的同时采取比传统意义上的轻量化技术更先进的方法和措施。
尤其在混合动力汽车领域,由于混合动力汽车的多样性和特殊性,使得整车结构设计和总布置存在很多困难,而且对整车质量的要求较传统汽车大大提高。为解决上述问题,结合混合动力汽车整车布置的具体情况,从汽车材料、结构特点等方面对混合动力汽车车身结构进行优化分析和设计,是实现混合动力汽车轻量化的关键。轻量化对新能源汽车是艰巨的任务,只有轻量化才能减少昂贵的电池重量,降低整车成本,从而接近市场需求。
另外,国家对新能源汽车的补贴也与单位载质量能量消耗量(Ekg)挂勾,轻量化是Ekg降低的重要手段,因此从车企角度,整车轻量化也是产品研发生产的方向。
2、新能源汽车轻量化的实现路径
汽车轻量化技术方法有很多,是一个系统工程。新能源汽车的轻量化应从以下两个重点方向开展工作:一是实现整车30%-40%以上的轻量化――抵消动力系统净增加的质量(适应现有可用的比能量较低的商品化能源);二是实现动力能源的轻量化――提高现有新能源的比能量或开发新的动力电源。只有这样,才能有效解决新能源汽车自身重量大、续驶里程短的问题。
电动汽车轻量化不仅是车身的轻量化,还包含传动设备、电池等。例如增加单位体积的电池容量以实现轻量化,目前对这一技术已能工程化。通过电池的重新排列布置也是提高系统能量密度的有效手段之一。例如通过对电芯尺寸的研究设计,与整车布置相匹配,更高效放置更多的电池,从而使电池箱体积不变,增加电芯数量,实现更长的续驶里程。
就整车制造而言,轻量化技术可以分为三个主要方面:材料、结构设计、制造工艺。
首先是应用高强度和轻质材料,比如高强度钢材、超高强度钢板、铝合金、镁合金、工程塑料及纤维增强复合材料等。其次是结构的轻量化优化设计,利用结构解析和CAD、CAE等技术进行结构的优化设计,以减少无用材料、减轻壁厚、减少零部件数量等。
第三是采用先进的制造工艺技术,如激光拼焊、辊压成形、高强度钢热成形、内高压成形等先进制造技术,结构胶粘接和异种材料铆接等先进连接技术。
其中,采用轻质材料是当前轻量化主流。
1)轻量化材料轻量化材料指的是低密度、高强度,在整车上应用后可提升单位面积承载质量的材料,最常用的如高强钢、轻质合金(铝合金、镁合金等)、非金属材料等。
高强度钢:我国普通高强度钢发展迅猛,车身使用比例接近50%,预计未来可以达到60-65%。超高强度和先进高强度钢材大幅落后,目前使用比例只有5%,预计未来将有3倍提升空间。综合来看,我国汽车HSS级以上钢材比例将从55%提升到70%以上,估计单车需求量增加30%左右。按照2015年33万辆新能源汽车销量,高强度钢消耗近16.5万吨。我们预计到2020年新能源汽车销量可达150万辆,高强度钢需求为75万吨,是当前规模的五倍。
铝合金:铝合金减重效果显著优于钢铁。汽车使用1kg铝可替代自重2.25kg钢材,减重比例高达125%,整个使用寿命周期内可减少废气排放20kg。以铝代钢的结构设计优化可以实现二次减重,效果可达直接减重的50%-100%。国产汽车用铝迎来战略机遇期。2014年中国汽车平均每辆用铝不到110kg,远低于北美的158kg/辆和欧洲的145kg/辆。预计未来五年CAGR高达10%,到2020年可以达到170kg/辆,单车使用量提升50%左右,车用铝材迎来快速成长的窗口期。
镁合金:镁是地球上储量最丰富的轻金属元素之一,蕴藏量丰富,在宇宙中含量第八,在地壳中含量丰度2%。含镁矿物主要来自白云岩、菱镁矿、水镁矿和橄榄石等。海水、天然盐湖水也是含镁丰富的资源。中国是世界上镁资源最为丰富的国家,镁资源矿石类型全,分布广,储量产量均居世界第一。密度小,比铝轻三分之一,其比强度(抗拉强度与密度之比值)较铝合金高,疲劳极限高,能比铝合金承受较大的冲击载荷,导热性好,铸造性好;尺寸稳定性好,易于回收,有良好的切削加工性,有较好的减振性能,在诸多方面比工程塑料优越,可替代工程塑料,在煤油、汽油、矿物油和碱类中的耐耐蚀性较高等。将是未来发展前景极为广泛的金属类材料。
玻纤复材:目前汽车厂商节能降耗压力大,汽车轻量化是实现节能降耗重要途径,玻纤增强热塑性复合材料是汽车轻量化主流材料。玻纤增强复合材料在性能、成本上优于普通塑料和铝合金等材料。一方面玻纤增强复合材料相比普通塑料的耐热性、抗冲击等指标领先,另一方面玻纤增强复合材料较铝合金等在成本上优势突出。目前我国玻纤增强复合材料市场主要以化工类企业为主,单一客户需求量有限,企业需要具备技术+销售结合的能力开拓新市场。目前总体来看大型企业偏少,集中度不高。
工程塑料:工程塑料具有突出的成型性、轻量化以及面对强烈撞击时能够缓冲吸能,已成为一个衡量一个国家汽车工业发展水平的重要指标。据统计,发达国家汽车的单车塑料平均使用量为120千克,占汽车总重量的12%-20%,而这个比例还将持续升高,预计到2020年,发达国家汽车平均用塑料量将达到500千克/辆以上。然而塑料刚度低、易老化,未来在车身大量运用仍面临不少安全隐患。
碳纤维:碳纤维力学性能优异,密度不到钢的1/4,抗拉强度却是钢的7-9倍,是唯一一种在2000℃以上的高温惰性环境中强度不下降的物质。宝马在i3和i8量产车上的大规模运用更是将碳纤维造车风潮推向顶峰。然而碳纤维也是一种脆性材料,一旦受力过大就会直接断裂,损坏后基本无法修复,而高昂的制造成本和回收费用更使得当前碳纤维的应用主要还局限于高端跑车、越野车和运动赛车上。
在新能源汽车领域,将以碳纤维复合材料为重点突破口,从基础研究和数据积累做起,从少量选装套件做起,逐步向车身覆盖件、结构件、功能键延伸。

在新能源汽车中,电池箱体材料的轻量化也成为近年来企业研发的热点。传统的电池箱体采用钢板、铝合金等材料铸造,然后对表面进行喷涂处理。而碳纤维具有较高的比强度,碳纤维与环氧树脂形成的复合材料密度仅为1.6kg/m3,是典型的高强度轻量化材料,并且其还具有优良的耐蚀性和阻燃性,因而在性能方面是传统金属材质电池箱体的理想替代品。
2)结构设计
在现代汽车工业中,CAD/CAE/CAM等计算机一体化技术在汽车的设计过程中起着非常重要的作用。利用CAD/CAE/CAM一体化技术,可以准确地对新能源汽车的实体结构和布局进行设计,对各关键构件板材厚度的变化进行灵活分析,并可从数据库中提取由系统直接生成的有关该车的相关数据进行工程分析及刚度、强度计算,实现对汽车零部件的精简、整体化和轻质化。同时,通过开发新能源汽车车身、底盘、动力传动系统等大型零部件整体加工技术及相关的模块化设计、制造技术,使新能源汽车从制造到使用各个环节都真正实现节能、环保。通过结合参数反演技术、多目标全局优化等现代车身设计方法,研究汽车轻量化结构的优化设计技术,包括多种轻量化材料的匹配、零部件的优化分块等。从结构上减少零部件数量,确保在汽车整车性能不变的前提下达到减轻自重的目的。
车身轻量化不是单纯的一味减轻质量,车身在轻量化过程中需要考虑很多方面,整车结构的安全性便是其中最重要的一点。由于目前国内外还没有统一制定新能源汽车的安全碰撞标准及其他安全指标,汽车生产企业在进行轻量化的过程中需要运用仿真软件ANSYS、CATIA、UG进行仿真设计,对轻量化设计后的车身进行结构刚度、材料疲劳性及安全碰撞等分析,从而提高新能源汽车的可靠性和安全性。
随着并行工程、计算机技术等现代工程技术的快速发展及其在汽车车身设计分析中的广泛应用,新能源汽车车身结构轻量化设计的发展呈现出以下特点:①结构设计与性能分析并行;②优化思想在设计的各个阶段均被运用;③虚拟仿真实验技术得以采用,并部分用于代替实物实验;④车身概念设计成为车身设计的一个重要阶段;⑤有限元法得到广泛应用。
3)制造工艺
在完成车身结构优化设计和选用轻量化材料之后,激光拼焊技术、热压成型技术等先进的加工制造工艺成为了是新能源汽车轻量化目标实现的关键因素,直接决定汽车轻量化应用的结果是否成功。
人们对新能源汽车的需求趋向于安全性更强、质量更轻且燃料利用效率更高等方面,先进高强度钢材、工程塑料及轻质金属等多种材料成为新能源汽车的重要车体结构材料。如果将上述材料单独使用,就会给最大限度减轻车体质量的潜能带来限制。通过粘接、铆接、翻边搭接、钎焊、螺纹连接等多种连接技术,巧妙地将上述多种减轻车体质量的材料结合在一起,能够克服安全性差、质量难以减轻和加工成本高等难题,从而为新能源汽车提供一种多材料优化组合的轻量化车身结构。
另外,新能源汽车制造中开始研究热冲压成形技术。热冲压成形技术是一个塑性变形和材料组织变化同时产生的工艺,因此塑性加工技术人员和材料开发技术人员必须比以往的冷加工成形研究更加密切协作。加热冷却技术必须结合新能源车身和底盘零部件的结构设计进行深入研究,以便可以实现零部件不同部位到达预期强度的要求。
3、新能源汽车轻量化前景
虽然轻量化材料的确能降低汽车的整体重量和碳排放量,但也大大增加了汽车的成本,目前新能源汽车轻量化的成本还没有具体量化的数据。车企及动力电池企业在轻量化方面更多的是在现有材料体系上减少用量,在设计与造型上作些改造,从而降低车重。轻量化材料应用方面国内还处于研发阶段,现有车型均没有批量化应用新型材料。新材料从实验到量产周期长,且研发成本高,企业还没有大规模地进行研发。目前主要是国外车企进行研发,国内大型车企也有相关技术储备,小企业处于跟风状态。
随着新能源汽车产品的成熟,产销量逐渐增多,成本也会随之下降,市场竞争将会围绕产品性能与品牌等方面展开,新能源汽车将直接与传统汽车竞争。随着消费者对汽车要求的提升,轻量化的需求也会越来越高,现在工艺及结构设计已不能满足整车对轻量化的要求,新材料的应用将会成为普遍现象。
往 ・ 期 ・ 精 ・ 选
(点击下方题目即可阅读)
我们擅长:
深圳振业企业管理咨询有公司服务宗旨:为注塑企业推广科学注塑、精益注塑的理念,推动注塑企业技术及管理的合理化、简单化、标准化。建立“高效、稳健、低成本、快反应”的工厂运作体系。提高生产效率,降低注塑制造过程中的变异,降低成本,缩短订单反应时间,减少现金流占用,最终增强注塑企业综合的竞争力!
--- THE END ---
精益注塑 zy-plas
精益注塑|专注于塑料行业服务
助力工厂改善致电:0755-28152581
振业注塑汇
海量的注塑干货,供您任意学习分享,注塑实战实例最多的公众号!
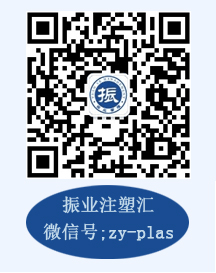
更多原创文章,请关注微信公众号:振业注塑汇
深圳注塑 www.szhenye.com 振业注塑 www.szhenye.com 杨建宏博客 http://blog.sina.com.cn/yangjianhong001