着眼于可持续发展,节约资源、减少环境污染成为世界汽车工业界亟待解决的两大问题。据统计,汽车每减重10%,油耗可降低6%~8%,因此减轻汽车重量是节约能源和提高燃料经济性的最基本途径之一。汽车轻量化正成为21 世纪汽车技术的前沿和热点。
汽车轻量化有两大途径:一是采用轻量化材料,例如采用铝合金、高强度钢材等强度更高、重量更轻的新材料;二是利用CAE 技术优化设计汽车的结构,使零部件薄壁化、中空化、小型化、复合化以及对零部件进行结构和工艺改进等以最大限度地减轻零部件的质量。以上两种途径是相辅相成的,必须采取材料替换与结构改进相结合的方法,才可能在保证汽车整体质量和性能不受影响的前提下,最大限度地减轻各零部件的质量。利用CAE 技术实现汽车轻量化有着传统设计手段不可比拟的优越性。
从汽车的总体构造来看,占汽车总质量比重较大的部分有车身、发动机、底盘、内外装备等。由此,车身、底盘、发动机等部件的轻量化研究对减轻汽车总质量存在很大潜力。
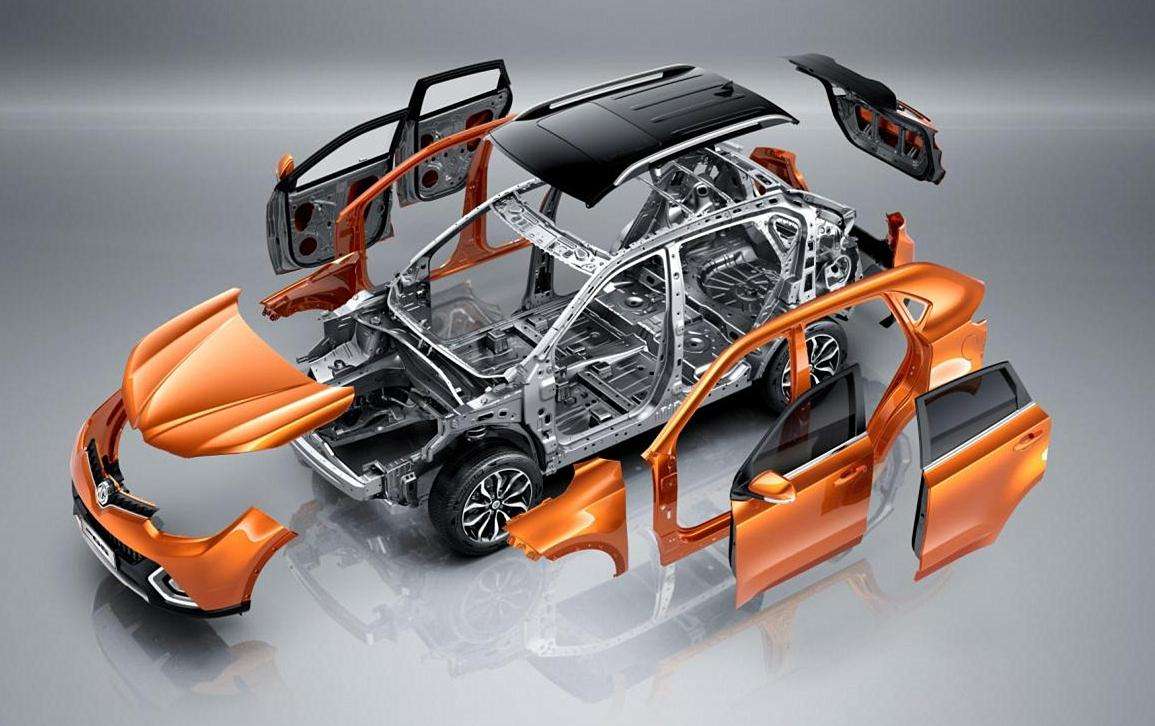
1 CAE 的技术概述
CAE ( Computer Aided Engineering, 计算机辅助工程) 技术是计算机技术和工程分析技术相结合形成的新兴技术,它的理论基础是有限元法和数值分析方法。
有限元法的基本思想是将连续的求解区域离散为一组有限个、且按一定方式相互连结在一起的单元的组合体。由于单元本身又可以有不同形状,因此可以模拟几何形状复杂的求解域。数值分析方法是研究适合于在计算机上使用的实际可行、理论可靠、计算复杂性好的数值计算方法,近40 年来,数值分析迅速发展并成为数学科学中的一个独立学科。
CAE 的核心技术为有限元技术与虚拟样机的运动/ 动力学仿真技术。主要是用计算机对工程或产品进行性能与安全可靠性分析,对其未来的工作状态和运行行为进行模拟,及早发现设计缺陷,并证实工程或产品未来性能的可用性与可靠性。参考文献将CAE 定义扩展为支持从研究开发到产品检测整个生产过程的计算机系统, 包括分析、计算和仿真在内的一切研发活动。
CAE 软件集成了有限元法、数值分析、优化设计、图像处理、工程管理学、人机智能工程等多种技术领域,是一种综合性、知识密集型信息产品,其中较为著名的有Nastran、Ansys、Abqus、Algor、Marc、Strand7 等。2000 年以来,CAE 软件在功能、性能、前后处理能力、单元库、解法库、材料库等方面进一步完善, 版本不断更新, 用户界面和数据管理技术等方面已臻于成熟, 解决了很多实际工程需要解决而理论分析又无法解决的复杂问题。
CAE 技术可以按目标分为静态分析、动态分析、可靠性分析和优化分析;根据研究对象的物理属性, CAE 又可以分为静力计算、动力计算、运动(干涉)计算、疲劳计算、热分析、流体分析、塑性分析及噪声分析等。
2 CAE 技术应用范围
CAE 技术的应用范围很广, 发展也相当快,CAE 技术的功能主要体现在产品的模型建立、工程分析、模拟仿真和优化设计等几个方面。
2.1 工程数值分析
运用工程数值分析中的有限元等技术分析计算产品结构的应力、变形等物理场量, 给出整个物理场量在空间与时间上的分布,实现结构的从线性、静力计算分析到非线性、动力的计算分析。分析内容包括静力分析和动力分析两个方面。静力分析通常包括: 线性、(材料、几何、状态)非线性静力分析;动力分析通常包括: 稳态动力分析、瞬态动力分析、谱分析。
2.2 仿真
运用运动/ 动力学的理论和方法, 对由CAD 实体造型设计出的机构、整机进行运动/ 动力学仿真,并给出机构、整机的运动轨迹、速度、加速度以及动反力的大小等。
2.3 结构优化设计
运用优化设计的方法在满足设计、制造、使用的约束条件下, 对产品的结构、工艺参数、结构形状参数进行优化设计, 使产品结构性能、工艺过程达到最优。
结构优化通常包括的截面优化、几何优化、拓扑优化、结构类型优化几个层次。
3 CAE 技术在汽车轻量化设计中的应用
在现代汽车工业中,CAE 技术在汽车设计中得到了广泛的应用,运用CAE 技术可以实现汽车的轻量化设计、制造。轻量化的手段之一就是对汽车总体结构进行分析和优化,实现对汽车零部件的精简、整体化和轻质化。
利用CAE 技术, 结合有限元法与结构优化方法,对零部件进行结构优化,是实现零部件轻量化的一个重要研究方向。本文从车身结构优化设计、发动机零部件优化设计、车架结构优化设计三个方面讲述了CAE 技术在汽车轻量化设计中的应用。
3.1 在车身轻量化设计中的应用
车身结构的轻量化对汽车节能和环保具有重要意义。据统计,客车、轿车和多数专用汽车车身的质量约占整车自身质量的40 %~60%。减轻汽车自身的质量,一方面节约了原材料,降低了汽车的生产成本,另一方面也降低了燃油消耗,有利于环保。随着计算机技术的发展, CAE 技术在车身轻量化设计上得到了广泛的应用。以下文献证明了车身设计轻量化的潜力。
YANG 等研究了基于有限元软件MSC /NASTRAN和CSA / NASTRAN 的汽车车身、底盘、焊点位置等的拓扑优化设计问题,通过优化设计,在减轻其车身重量的前提下, 并提高其承载能力和抗变形能力。WANG 等利用有限元法与拓扑优化方法对汽车车身的加强筋部分进行了优化,通过优化设计,在既定成本下汽车车身的整体刚度能够得到充分的提高。
FREDRICSON 等对拓扑优化设计在汽车设计中的应用作了综述, 重点介绍了车身设计的拓扑优化进展和存在的问题。高云凯等把拓扑优化设计理论引入某电动改装车的承载式车身设计, 利用先进的有限元分析软件, 在电动改装轿车车身结构拓扑优化分析中实现了多工况、多状态变量条件下的拓扑优化设计,确定了下车身的最佳结构方案,进而在此基础上建立了新的有限元模型,并进行了模态、刚度和强度分析,设计出最终的下车身改造结构,优化后下车身质量为初始基本拓扑结构的10%。陈茹雯等利用基于有限元法的拓扑优化技术设计车身大骨架的拓扑结构, 对优化后的车身骨架模型进行有限元分析,将其动、静特性参数与原设计作比较。研究表明, 经拓扑优化后的车身大骨架各项特性参数指标均有不同程度的提高。优化后的车身刚度比原有的车身刚度提高了1.35 倍。优化后的车身质量比原有的车身质量减少了25.65%。于兴林等基于有限元法的拓扑优化技术,将优化提前到车身大骨架的初始划分阶段, 找出其结构最优拓扑解,进行了车身结构的优化设计。最后以拓扑优化的结果为依据,开发了一种结构更安全、更轻量化的新型的车身结构。
可见,采用CAE 技术结合有限元法正成为车身轻量化设计中结构优化的重要手段,更广泛的应用还有待进一步研究。
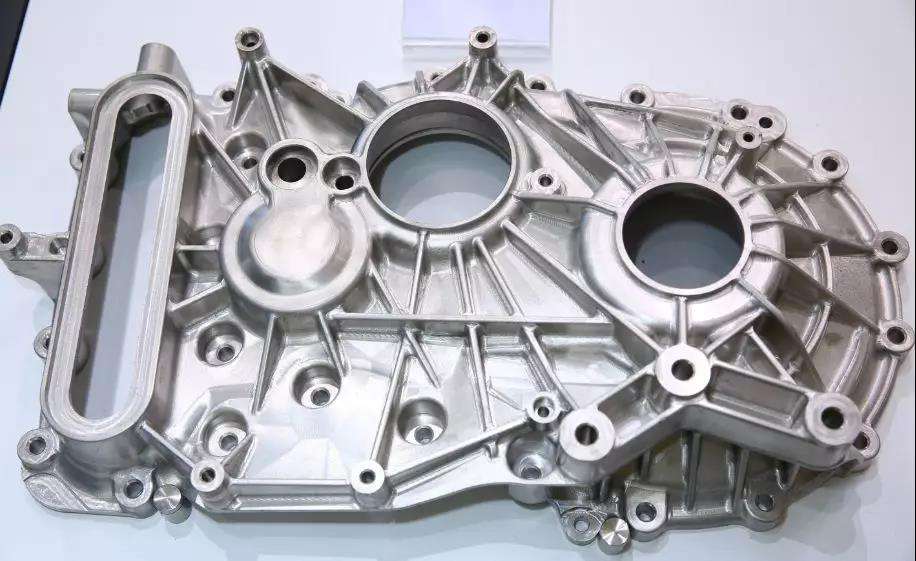
3.2 在发动机零部件轻量化设计中的应用
发动机是整个汽车的动力来源,随着新型汽车的不断发展,对发动机的要求也越来越高,要求现代发动机有高效率、高可靠性、体积小、质量轻的同时要求有低燃油消耗率和低排放等。发动机作为汽车最为关键的大总成之一,减轻发动机的质量对降低汽车自身重量也至关重要。从总的趋势上看,发动机一直在向着轻量化的方向发展,CAE 技术在发动机设计领域也得到广泛应用。
采用CAE 技术的拓扑优化的方法,可以在刚度不变的情况下减轻质量, 或质量不变的情况下提高刚度。目前,拓扑优化方法主要应用于主轴承盖、连杆盖等的优化设计,并取得了令人满意的效果。奥迪公司应用拓扑软件进行发动机支架优化, 在自振频率提高30%的情况下质量减轻了20%; 而在进行主轴承盖优化设计中,质量减轻了22%。福特公司应用拓扑优化手段使连杆应力降低了17%而保持质量不变。国内制造商也已经开始应用拓扑优化结构设计,如第一汽车集团公司在某新型发动机设计中, 应用拓扑优化对采用经验方法设计的发动机支架进行了结构优化,在最大应力不变、刚度提高的情况下,零件的质量减轻了10%。王宏雁等采用拓扑方法优化、改进结构,并通过有限元结构模拟计算,对汽车发动机罩进行了优化设计。张宇等采用有限元法以某型多功能乘用车为对象,结合材料替换与结构改进对该车的发动机罩内、外板进行轻量化设计,同时解决了实车碰撞试验中发动机罩铰链发生断裂的问题。轻量化设计的发动机罩板满足了静态刚度设计要求及整车耐撞安全性能,发动机罩内、外板的减重效果分别为46. 38%和50.18 %。李红建等以发动机罩内板动态优化为对象,介绍了拓扑优化设计的基本过程,对优化前后结构性能进行对比分析,产品试验数据证明了优化结果的可靠性。
CAE 技术的拓扑优化在发动机零部件轻量化设计中应用已经比较成熟,更广泛的应用还有待进一步研究。
3.3 在车架结构轻量化设计中的应用
汽车车架是汽车结构件中结构和载荷都很复杂的重要部件,也是人们首先开展结构分析和结构优化设计的研究对象。近年来, 随着CAE 技术的发展, 拓扑优化技术成为以提高结构性能或减轻结构质量为目标的一种新兴结构设计方法, 随着商业有限元分析软件,如ANSYS,NASTRAN 中拓扑优化功能的实现,以及商品化结构优化软件(如OptiStruct,TOSCA 等) 在国内的逐步普及,目前已在车架轻量化设计中得到成功应用。
例如Altair 公司技术报告表明,在SUV 车架轻量化设计中,结构优化技术涵盖了从概念设计阶段、基本设计阶段到详细设计阶段的全流程, 在概念设计阶段起主要作用的拓扑优化技术得到了全面展示。王健等研究了薄板应力约束下的变厚度法,并给出了运输车车架拓扑优化设计的工程应用实例。刘齐茂基于ANSYS 软件,综合运用拓扑及尺寸优化技术, 对某型载货车车架车架进行拓扑优化获得车架最优拓扑形式, 根据车架最优拓扑形式确定横梁的数量及分布位置和纵梁的加强方式, 实现了车架的轻量化设计。石琴等探讨了拓扑优化设计过程中,拓扑优化模型建立、优化过程控制及优化结果分析与应用问题, 并在ANSYS 软件平台上进行了CAE 软件包的二次开发,设计了集装箱半挂车车架优化设计专用软件模块。在结构设计的开始阶段引入拓扑优化理论,先对结构进行布局优化,以获得较合理的初始结构方案, 再通过结构参数优化设计, 得到满足其强度和刚度及设计工艺要求的最优结构。杨树凯等用变密度法建立了汽车支架结构拓扑优化数学模型, 利用有限元法进行了结构拓扑优化设计。赵韩等采用有限元法对某型号半挂汽车车架结构的应力分布进行了分析, 形成了车架的初始设计方案, 进而从有限元分析的结果出发形成优化设计即轻量化设计所需要的数学模型。并在对有限元模型进行试验验证的基础上, 提出了该车架结构的轻量化设计方案并进行了有限元强度分析,确定了较合理的车架轻量化设计方案。桂良进建立了某型载货车车架结构的应力分析有限元模型,计算了多种工况下车架结构的应力分布并以已有的试验结果进行验证。在此基础上,提出该车架结构的轻量化设计方案, 并进行了改进设计后车架结构的强度分析,确定了合理的轻量化设计方案。苏庆等运用CAE 技术对某微型客车车架进行了结构分析与优化设计,首先计算了静力挠度, 静态弯曲、扭转刚度, 然后求解了固有模态, 并在此基础上获得典型道路激励下的瞬态响应, 此外, 还对车架典型薄壁梁结构的耐撞性吸能特性进行研究, 配合实验数据, 对车架结构进行了合理的改进设计, 实现了满足轻量化要求的静态优化设计目标。
由此,CAE 技术在各种特性车的车架的轻量化设计研究中得到了广泛的应用,并取得了显著效果。
4 结语
综合国内外已经开展的研究,采用CAE 技术在汽车结构轻量化的理论研究和实际应用都取得了重要的进展。无论是从方案设计、方案评价、模型建立、工程分析等诸多方面实现对汽车零部件的精简、轻质、整合,还是对轻量化后汽车的操纵稳定性、强度和刚度、行驶安全性、乘坐舒适性等性能指标进行分析与评价,最终都实现减轻汽车质量,提高燃油经济性, 减少排放污染的目标。彰显了CAE 技术在汽车研发过程中的作用日益重要。(文章来源:网络,版权归原创所有,如侵权联系删除)
往 ・ 期 ・ 精 ・ 选
(点击下方题目即可阅读)
我们擅长:
深圳振业企业管理咨询有公司服务宗旨:为注塑企业推广科学注塑、精益注塑的理念,推动注塑企业技术及管理的合理化、简单化、标准化。建立“高效、稳健、低成本、快反应”的工厂运作体系。提高生产效率,降低注塑制造过程中的变异,降低成本,缩短订单反应时间,减少现金流占用,最终增强注塑企业综合的竞争力!
--- THE END ---
精益注塑 zy-plas
精益注塑|专注于塑料行业服务
助力工厂改善致电:0755-28152581
振业注塑汇
海量的注塑干货,供您任意学习分享,注塑实战实例最多的公众号!
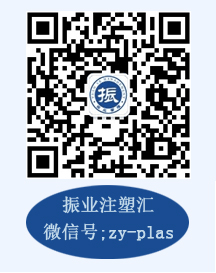
更多原创文章,请关注微信公众号:振业注塑汇
深圳注塑 www.szhenye.com 振业注塑 www.szhenye.com 杨建宏博客 http://blog.sina.com.cn/yangjianhong001