锁模力这个参数是注塑生产中的一个基本参数,锁模力大小关系到下列方面:
1.直接影响模具排气与焦烧缺陷
2.直接影响披锋
3.间接影响熔接线
4.对注塑压力速度的影响会涉及几乎所有的缺陷
5.直接影响模具寿命
6.直接影响注塑机锁模系统的耐受性及寿命,方法锁模系统的问题
7.直接影响机器哥林柱的寿命
8.间接影响生产安定化程度
正因为此,注塑厂生产中特别关注锁模力,但大型模具因为在生产后机器变热,模具膨胀会导致锁模力变化增加而不得已要二次调模。
为什么要二次调模呢,上面已经说了,模具膨胀锁模力变化了。
那今天我就量化地试算下模具膨胀多少?
查表知道,铁的线性热膨胀系数是大约1.2*10-5/℃。如果一个模具0.8米厚,常温20度,加热油120度且生产稳定。
1、不是模具浑身都一起受热的,模芯最热,同时模具的垫脚 动模固定板 推板推板固定板温度较低。这部分的温升及膨胀暂时忽略。这部分去掉后,可能膨胀的模具厚度大约是0.5米。
2、这时候其他区域并非都是120度。最热的就是型腔表面附近。我们简化一下,0.5米厚的模具一半靠近中间的(靠近分型面的)取120度,外侧两半取80度(以前生产中实测数据大约如此)
- 下面我们计算膨胀的伸缩量:
1.2*10-5/℃*(250mm*100℃(温度差) 250mm*60℃(温度差))=0.48mm
所以,模具在刚上机常温时候和正常生产时候的厚度差是0.48mm。
- 这里要注意的是,有人喜欢在模具上机器后还没有升温就调模,那厚度差异就是0.48mm,这样的厚度差会导致锁不上模。
- 有人进一步,等模具温度上来了再调模,但这时候只是水路附近的局部(包括型腔面)温度上来了,但模具框架的其他部分温度还没有上来,如果这样的话,第一次调模后,厚度差异会少点,但也要>0.2mm,这样的厚度也会导致锁不上模。
- 为什么呢?
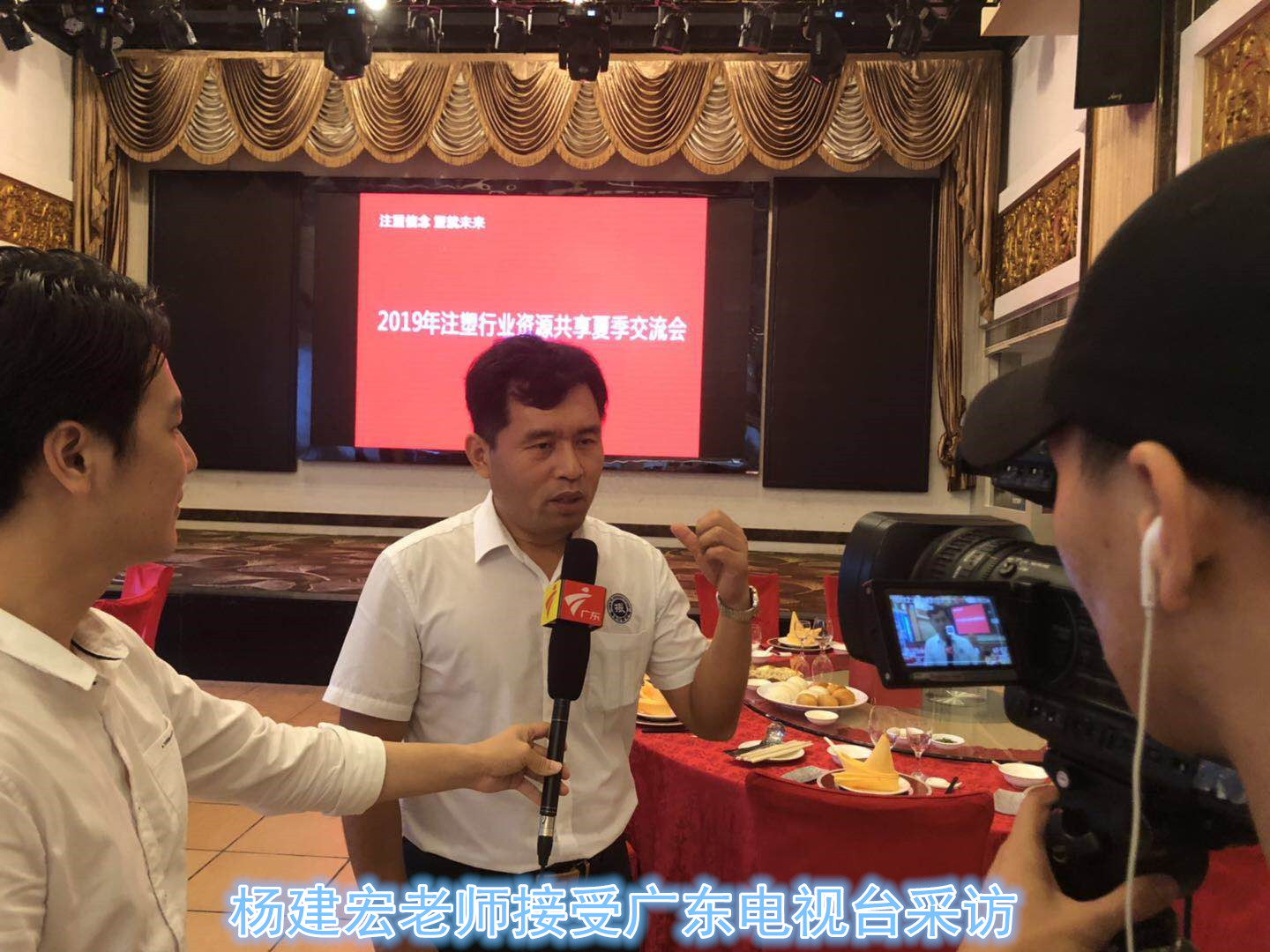
模具起高压前,低压保护的的理想位置在0.05~~0.2mm,所以还是起不了高压,锁不上模具。
当然了,锁不上模具是模具线性膨胀,锁模力增加的最高形式,在此之前,由于锁模力已经增加了,会发生很多潜在的影响,就像文章开头说的那8点一样。
本例中,0.8m厚已经是很大的模具了,一般的小模具不会有这样的形变量,所以一般在生产中,大的模具在生产一段时间,温度稳定了,都要重新调模。
这是个很精细的需要特别关注的工作小环节。幸好,现在技术发到,许多机器已经有了锁模力自动监控及动态的自动调模功能,比如sumitomo,JSW等,这样的机器就不用麻烦人工调了。