我们常用的浇口形式有下列11种。
1. 直浇口:即是主流道浇口,属于非限制性浇口,
(1)优点:塑料熔体由主流道的大端直接进入型腔,因此具有流动阻力小、流程短及补给时间长等特点。这样的浇口有良好的熔体流动状态,熔体从型腔底面中心部位流向分型面,有利于排气;这种浇口形式使注塑制品和浇注系统在分型面上的投影面积最小,模具结构紧凑,注塑机受力均匀。
(2)缺点:进料处有较大的残余应力,容易导 致注塑制品翘曲变形,同时浇口较大,去除浇口痕迹较困难且痕迹较大,影响美观,所以这类浇口多用于注射成型大中型长流程、深型腔、筒形或壳形注塑制品,尤其适合于聚碳酸酯、聚砜等高粘度塑料。另外,这种形式的浇口只适合于单型腔模具。
在设计这类浇口时,为了减小与注塑制品接触处的浇口面积,防止该处产生缩口、变形等缺陷,一方面应尽量选用较小锥度的主流道锥角(为2~4°),另一方面应尽量减小定模板和定模座的厚度。
2. 侧浇口:国外将侧浇口称为标准浇口,见图2。侧浇口一般开设在分型面上,塑料熔体从内侧或外侧充满模具型腔,其截面形状多为矩形(扁槽),改变浇口宽度与厚度可以调节熔体的剪切速率及浇口的冻结时间。这类浇口可根据注塑制品的形状特征选择其位置,加工和修整方便,因此它的应用较广泛。
(1)优点:浇口截面小,能减小浇注系统熔料的消耗量,去除浇口容易,痕迹不明显。适合于各种形状的注塑制品,但对细长桶形注塑制品不宜采用。
(2)缺点:注塑制品和浇口不能自行分离,存在熔接痕,注塑压力损失较大,对深型腔注塑制品的排气不利。
3. 扇形浇口:扇形浇口如图3所示,一般开设在分型面上,从型腔外侧面进料,浇口沿进料方向逐渐加宽,厚度则逐渐减薄。从浇口进入型腔的塑料熔体波前较为平直,可减少翘曲变形,用来成型宽度较大的板状塑料制品颇为适宜。
4. 薄片浇口:又称为平缝式浇口,见图4。浇口的分配流道 与型腔侧边平行,其长度通常大于塑料制品宽度。
(1)优点:塑料熔体通过薄片浇口以较低的速 度均匀地进入型腔,其料流呈平行流动,可避免翘曲变形,常用来成型平直的大面积薄壁塑料制品。
(2)缺点:去除浇口较为困难,从而增加了塑料制品的生产成本。
5. 护耳浇口:护耳浇口(见图5)主要用于高透明的平板形塑料制品及变形要求很小的塑料制品。
(1)优点:护耳浇口是在型腔侧面开设耳槽,熔体通过浇口冲击在耳槽侧面上产生摩擦热,从而 改善了流动性,经调整方向和速度后,在护耳处均匀而平稳地进入型腔,可以避免喷流。
(2)缺点:浇口切除较为困难,浇口痕迹较大。
6. 点浇口:点浇口尤其适用于圆桶形、壳形及盒形塑料制品。对于较大的平板形塑料制品可以设置多个点浇口,以减小翘曲变形;对于薄壁塑料制品,浇口附近的剪切速率过高,残余应力大,容易开裂,可局部增加浇口处的壁厚,如图6所示。
(1)优点:点浇口位置限制小,浇口痕迹小,开模时浇口可自动拉断,有利于自动化操作。
(2)缺点:注塑压力较大,多数情况下必须采用三板模结构,其模具相对较复杂,成型周期较长。
7. 潜伏式浇口
(1)优点:潜伏式浇口(见图7)位置比较灵活,可在塑料制品内外表面进胶。流道开设在分型面上,浇口潜入分型面下,熔料斜向进入型腔。由于在塑料制品和流道分别设置推出机构,开模时浇口自动被切断,流道凝料自动脱落。同时其模具结构较三板模结构简单,大大提高了生产效率并可降低成本。
(2)缺点:对过韧(如PA类)或过脆(如PS 类)的塑料并不适用,前者不易切断,后者易于断裂,容易堵塞浇口。
8. 月亮形浇口:月亮形浇口(见图8)其实是一种圆弧形潜伏式浇口的结构形式,一般用于二板模,采用分型面直接进胶方式,制成两块镶件拼合,其分流道及浇口都设计在镶件上。
(1)优点:可在制品底面进胶,具有点浇口的特点,浇口痕迹小,顶出时能自动拉断,容易实现自动化。如将其顶出销头部做成锥形,在流道设置推出机构,有利于顶出。(2)缺点:形状较复杂,需要用电极加工浇口。
9. 环形浇口
对型腔填充采用圆环形进料形式的浇口称为环形浇口,如图9所示。
(1)优点:进料均匀,圆周上各处流速大致相 同,流动状态好,容易排除型腔中的空气,并可避免熔接痕。由于浇口设计在型芯上,环形浇口主要用于成型圆筒形无底塑料制品。
(2)缺点:浇注系统耗料较多,浇口去除困难,浇口痕迹明显。
10. 伞形浇口:伞形浇口(见图10)是环形浇口的特殊形式,主要应用于质量要求很高的短粗管形塑料制品。
(1)优点:进料均匀,无熔接痕产生,排气良好。
(2)缺点:去除流道必须采用切削加工,增加了成本。
11. 盘形浇口:盘形浇口(见图11)实际上是顶角为180°的伞形浇口,用于内孔较大的圆筒形塑料制品,或具有较大长方形内孔的塑料制品,浇口在整个内孔周边上。
(1)优点:具有伞形浇口的特点,塑料熔体从内孔周边以大致同步的方式注入型腔,型芯受力均匀,可以避免熔接痕,排气顺畅。
(2)缺点:会在塑料制品内缘留下明显的浇口痕迹。
二. 常见塑料制品进胶形式选用
(1) 轴向对称制品:像齿轮、叶片之类的制品在工作中转速较高,表面应光滑平整、无气泡等以保证耐磨性,这类制品要求功能面(一般是侧面)不能有缺陷,底面需要平整,所以这类制品的浇口要尽量小,且要做得隐蔽,故不适合用潜伏式浇口(包括潜顶针)及其它去除浇口困难的形式。最好使用月亮形浇口,或者使用三板模具,设置点浇口以获得良好的流动特性。
(2) 管形制品:应使熔料首先填充一端的圆周,然后再填充管本身的全长部分。这样可使熔料流动前沿避免产生不对称形
状。常用盘形浇口、伞形浇口、环形浇口及潜伏式浇口形式。
(3)杯形制品:像小壳体、电容器杯之类,浇口应设计在底座附近,以避免产生空气穴。一般常用点浇口或潜伏式浇口潜到底座附近。
(4)细长制品:应该沿纵向而不是沿横向,或在中心设置浇口,一般常采用侧浇口、潜伏式浇口及月亮形浇口。
(5)轮辐式或网状制品:采用多点浇口形式。
(6)一体式铰接制品:应使熔接痕远离铰接点。在任何情况下都应避免将熔料停止流动部分设计在铰接点附近,可采用侧浇口或潜伏式浇口。
(7)透明塑料制品:为了避免制品出现蛇纹等缺陷,常使用护耳浇口。
(8)电镀塑料制品:采用侧浇口连同塑料制品一起顶出,在流道上做电镀挂点,电镀完毕即去除浇口。
(9)薄壁制品:点浇口适用于薄壁制品,若以高速注射,可能会出现喷射的情形。将浇口设置在制品最厚部位,且要保持厚度均匀,以免导致变形。
(10)扁平塑料制品:常采用扇形浇口或薄片浇口。这类浇口进料均匀,无熔接痕产生,排气良好。
(11)带金属嵌件的塑料制品:使熔料能够在镶嵌件周围流动,以尽可能减少镶嵌件位置的不准 确性。经常采用侧浇口或者潜伏式浇口。
三. 浇口位置选择原则
浇口位置主要是根据制品的几何形状和技术要求,并分析熔体在流道和型腔中的流动状态、填充、补缩及排气等因素后确定的。一般应遵循如下原则:
① 浇口应设在塑料制品断面较厚的部位,使熔料从厚断面流入薄断面以保证充模完全;
② 使熔料充模流程最短,流向变化最小,能量损失最小,以减少压力损失;
③ 有利于排除型腔中的空气;
④ 浇口不宜使熔料直接冲入型腔,否则会产生漩流,在塑料制品上留下螺旋形的痕迹,特别是窄的浇口更容易出现这种缺陷,最好从正对型腔壁或粗大型芯的方位进入,改变流向,以低的流速平稳地充满型腔,可避免熔体破裂现象,消除塑料制品上的熔接痕;
⑤ 应防止在塑料制品表面产生熔接痕,特别是对圆环或圆筒形的塑料制品,应在浇口面的熔料浇合处加开冷料井;
⑥ 带有细长型芯注塑模的浇口位置,应当离成型芯较远,不得使成型芯受料流冲击而变形;
⑦ 大型或扁平塑料制品成型时,为防止翘曲变形和缺料,可采用复式浇口;
⑧ 浇口应尽量开设在不影响塑料制品外观的位置,如边缘、底部;
⑨ 设计多型腔注塑模时,结合流道的平衡来考虑浇口的平衡,尽量做到熔料 同时均匀地充满各型腔。
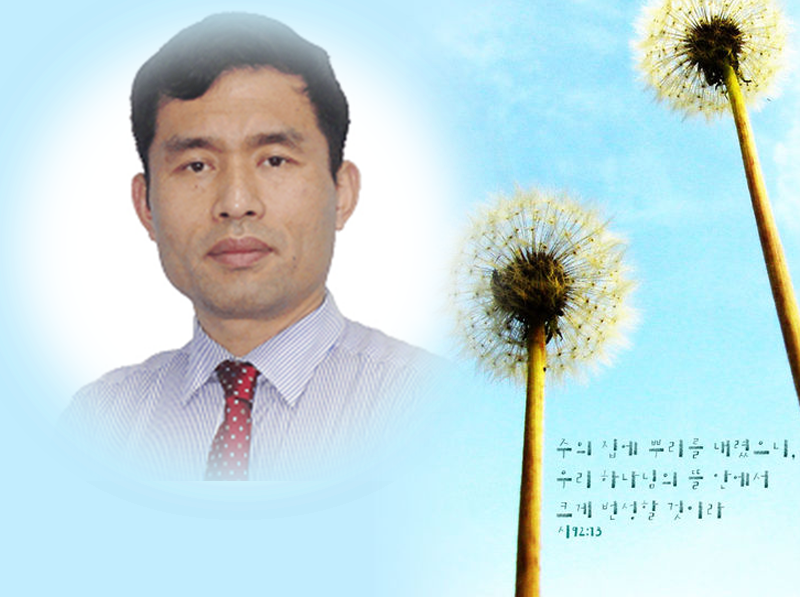
最后的叮叮咛
我们应该注意哪些?
浇口的设计与位置的选择恰当与否,直接关系 到塑料制品能否被完好、高质量地注射成型。浇口的形式和开设的位置不仅会对塑料制品的成型性能及成型质量有很大影响,而且还会影响到模具的整体结构。因此,合理地选择浇口形式和开设位置是提高塑料制品质量的一个重要环节。选择浇口形式和位置时,需要根据塑料制品的结构、工艺特征和成型质量要求,并分析塑料原材料的工艺特性、塑料熔体在型腔内的流动状态及成型的工艺条件综合加以考虑。